COVID-19: A Catalyst for M4.0 Culture
The pandemic has spurred a paradigm shift in cultural transformation as manufacturing companies have leveraged M4.0 to accelerate digital adoption, collaboration, innovation, and integration across their enterprises, reveals the Manufacturing Leadership Council’s latest M4.0 Cultures survey.
By Sue Pelletier
It’s undeniable that the COVID-19 pandemic has caused massive disruption in the manufacturing environment over the past year. Supply chain disruption, already a growing problem pre-pandemic, became more acute as different areas of the world shut down to slow the spread of the virus. Some manufacturers pivoted to retool their factories to supply much-needed personal protective equipment (PPE) and other COVID-necessitated supplies, while others struggled to keep shop floor workers safe and learned on the fly how to manage employees who suddenly had to work remotely.
The impact on manufacturing cultures has been significant. The results of the Manufacturing Research Council’s latest M4.0 Cultures survey reveal that the abrupt shifts and continued disruptions of the COVID-19 crisis have driven leaders to sharpen their focus on M4.0 and accelerate adoption across everything from enterprise connectivity and corporate collaboration, to functional integration and innovation, and to start redefining what health and safety should mean for their employees in the future.
What’s more, while some of the workforce cultural changes, such as PPE and masking for front-line employees, may be temporary, the survey results clearly indicate that a major shift toward an M4.0 culture that is digitally enabled, collaborative, innovative, and data-driven is not only underway more rapidly than ever before, but is also here to stay.
There will continue to be a few bumps in the road ahead, of course. While corporate cultures are increasingly becoming more customer-centric and collaborative, the journey toward M4.0 is still a work in progress for many companies as concerns about the costs and ROI of M4.0 transformation, along with getting full buy-in from both employees and leadership, stubbornly continue to impede the progress of cultural changes. But it is clear that the COVID viral firestorm has made manufacturers acutely aware of the need to continue along that M4.0 journey. With many saying the recent changes in their corporate culture will now be permanent, it’s clear that they are already beginning to see the results, from improved morale and a more efficient workforce, to more productive and innovative operations. And those are exactly the kinds of benefits that will spur them to continue to overcome any remaining hurdles.
“Manufacturers now believe that the M4.0 paradigm shift that has accelerated over the past year has led to permanent changes that will have a lasting impact on their organizations for many years to come.”
Culture Change Accelerates During COVID
While it might be expected that the pandemic’s disruptions could have slowed the adoption of digital M4.0 plans, that turned out not to be the case. As leadership teams have intensified their focus on M4.0 over the past year (Chart 2), more than half said they have accelerated both enterprise connectivity and M4.0 technology adoption since COVID-19 hit (Chart 1). Corporate collaboration initiatives also sped up for more than 50% of companies, with ramped up functional integration strategies and faster innovation processes also reported by more than 40% of survey respondents.
While COVID has clearly had a significant impact on many areas of corporate culture, one of the key takeaways from the survey is that these are not quick fixes to patch operations until the crisis passes. The results make it clear that manufacturers now believe that the M4.0 paradigm shift that has accelerated over the past year has led to permanent changes that will have a lasting impact on their organizations for many years to come.
For example, one of COVID’s biggest impacts on corporate culture has been an increased use of digital collaboration tools and platforms, which a full 79% ranked as “significant” (Chart 3). An overwhelming 85% said this change is likely to be permanent. Another change spurred by the pandemic that the majority expect to become permanent is the shift toward increased focus on disaster preparedness and crisis management.
Other significant changes slated to become permanent fixtures in corporate culture for many include more regular and open top-down communication with employees, more collaboration between teams who did not previously work together, and an increased sense of purpose and shared values among working teams. Improved employee feedback and communication from the bottom up, while not as widely instituted, is a change almost half of those who have made improvements plan to make permanent.
“The survey results clearly indicate that a major shift toward an M4.0 culture that is digitally enabled, collaborative, innovative, and data-driven is not only underway more rapidly than ever before, but is also here to stay.”
While widely implemented pandemic-specific health and safety shifts such as PPE and mask requirements are only planned to become permanent for a quarter of respondents, health and safety strategies are being extensively redefined and are going to mean much more than just accident prevention moving forward, said 61% (Chart 4). Seventy percent of those who shifted to remote and virtual work strategies also say they intend to enable at least some of their workforce to continue working from home in the future. This also reflects the increasing use of digital collaboration tools and platforms that make remote work feasible for many more employees, and which will continue to move companies toward creating a more empowered, collaborative, and responsive workforce for the future.
M4.0 Culture Moving into the Mainstream
The shift toward a more M4.0-based overall corporate culture is evident in the terms manufacturers now use to describe the current state of their corporate cultures, with customer-centric and collaborative topping the list. (Chart 5). What is clear, however, is that there is a strong belief that continued culture change will be essential in the digital age, with a substantial 71% saying they will need to continue to transform their cultures in the future to fully take advantage of all the M4.0 era offers (Chart 6). For example, 60% consider a move toward more data-driven decision-making should be on top of their change agenda, and more than half believe better integrated, more cross-functional teams would help drive future success. Increased responsiveness, more agile operations, faster innovation and time-to-market for new products, and even more of an emphasis on customer and supplier centricity are also likely to be key elements of necessary culture change (Chart 7).
Many of those changes are already underway. Thirty-seven percent now say they are either satisfied with their current culture or actively working to make the needed changes, up from 24% in 2019 (Chart 8). While these changes may be incremental, there are still many ongoing challenges to cultural transformation, with top concerns such as cost/ROI and a lack of leadership bandwidth/buy in dominating the list, followed by a lack of employee buy-in and no formal strategy.
Collaborative Cultures on the Rise
With almost unanimous agreement that a collaborative culture is either very or somewhat important to future competitiveness, and three quarters (74%) identifying it as necessary for competitive survival, it is evident that collaboration is top of mind for today’s manufacturers (Chart 10). While the immediate needs of dealing with the pandemic likely led to the slight rise in traditional command-and-control hierarchical structures in some organizations, from 30% in 2019 to 34% in 2021, only 14% of manufacturers predicted that this approach would still hold true two years from now. Even more telling is the rapid rise of those who describe their culture as collaborative, which went from 17% in 2019 to 26% in 2021, and is predicted to surge to a substantial 51% by 2023 (Chart 9).
The key enablers to achieve that desired collaborative culture, according to 61% of respondents, are M4.0 technologies and approaches (Chart 11). This is reflected in the significant increase in the adoption of digital threads across all company functions over the past two years. In manufacturing operations, for example, the use of digital threads shot up from 45% in 2019 to 70% of companies today, while supply chain digital threads are now being used in 50% of organizations (up from 35% in 2019), and further increases are evident in design and engineering, IT, and even in more customer-focused areas such as sales and marketing and customer service and support (Chart 12).
M4.0 Drives Faster Innovation
Innovation processes have also accelerated in many manufacturing companies over the last two years, with 25% saying they are continually developing new products and embracing change, up from just 19% in 2019. More than half aren’t far behind, defining their culture as “moderately innovative,” and being willing to experiment with new technologies, products, and services (Chart 13). Perhaps most importantly for the future though, almost three-quarters of companies now credit M4.0 technologies and approaches as key drivers to faster and more effective innovation in the years to come (Chart 14).
The source of ideas for these new products, processes, and/or business models has also shifted slightly since 2019, with suppliers kickstarting innovation for 47% of manufacturers, up from just 28% two years ago (Chart 15). External partners and academic and research institutions also are taking on an increasing role in innovation. But, that pales in comparison to the growing role of company employees, whom 86% of manufacturers now credit as the source for new ideas, compared to 74% in 2019.
“While many were already on the road toward M4.0 before the pandemic hit, COVID-19 proved to be a wake-up call that the time is now to start implementing the changes to corporate culture needed for today’s, and tomorrow’s, manufacturers.”
M4.0 Essential to Integration
The flattening of corporate hierarchies, the elimination of siloes, and the increase in communication and cross-function and cross-training in the workforce are resulting in an increasingly integrated business. More than a third of companies in the survey say they have already made significant changes to become more integrated, up from less than a quarter in 2019 (Chart 16).
As with collaboration, M4.0 technologies and approaches also are regarded as essential ingredients to successful integration, according to 69% of respondents (Chart 17). But when it comes to integrating IT and OT teams, there’s still some progress to be made. While more than half now have at least somewhat integrated OT and IT functions, up from 43% in 2019, only 16% say these areas are fully integrated so far (Chart 18).
Creating a more integrated enterprise remains challenging, however. Issues around effectively managing cultural/behavior change, having the leadership time and focus to change operations while still running the business, and developing the consensus needed for an implementable overall strategy, continue to be the most significant barriers to integration. However, the latest survey also suggests there also growing concerns over getting buy-in from heads of functional areas, understanding the benefits, and obtaining funding and resources to make it happen (Chart 19).
While many were already on the road toward M4.0 before the pandemic hit, COVID-19 proved to be a wake-up call that the time is now to start implementing the changes to corporate culture needed for today’s, and tomorrow’s, manufacturers. The key to future success will be to keep that momentum, born in many cases of necessity, going once the immediate crisis subsides. The role of M4.0 in that continued transformation now seems abundantly clear. M
Part 1: COVID-19 Impact
1 COVID-19 Has Accelerated M4.0 Transformation Across Multiple Areas
Q:What impact has COVID-19 had on your M4.0 transformation strategy in the following areas?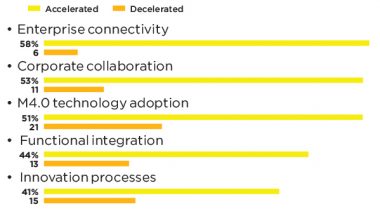
2 50% Say COVID-19 Has Also Increased Leadership Focus on M4.0
Q: What impact has COVID-19 had on your leadership team/management’s focus on digital/M4.0 transformation?
3 85% Expect Increased Use of Digital Collaboration Tools to Be Permanent
Q: What impact has COVID had on your corporate culture, and how long do you expect these impacts to continue?
4 Working Cultures Shifting to Remote, Safer Strategies for Employees
Q: What impact has COVID-19 had on your workforce culture, and how long do you expect these impacts to continue?
Part 2: Overall Company Culture
5 Corporate Cultures Increasingly Customer-Centric and Collaborative
Q: What term would you use to describe your company’s culture today?
6 Strong Majority Believe Culture Change Needed in Digital Era
Q: Thinking about the requirements of the digital age, does your company believe it needs to change its culture to embrace this new era?
7 Data-Driven Decision-Making & Functional Integration Top Culture
Change Agenda
Q:If a culture change is needed, which description would best capture what that change would encompass?
8 ROI Concerns & Leadership Bandwidth Remain Key Challenges to Change
Q: What are your company’s biggest challenges
to cultural change?
Part 3: Collaboration
9 51% Predict Collaborative Structures Will Dominate in 2 Years
Q: How would you describe your overall corporate structure today, and where do you expect it to be in 2 years’ time?
10 Three Quarters Say Collaboration is Essential to Competitiveness
Q: How important do you think a collaborative
culture is for competitiveness?
11 M4.0 Key to Enabling a Collaborative Culture
Q: Is there a clear belief that M4.0 technologies and approaches are key to enabling a more collaborative culture?
12 Extensive Adoption of Digital Threads Across All Functions in Last 2 Years
Q: Which of your company functions are connected to a digital thread to enable end-to-end data sharing and collaboration?
Part 4: Innovation
13 Three-Quarters Say They Are Already Moderately to Highly Innovative
Q:How would you describe your company’s current level of innovation?
14 Almost Three-Quarters Believe M4.0 is Key to Driving Innovation
Q: Is there a clear belief that M4.0 technologies and approaches are key to enabling faster and more effective innovation?
15 Increasing Role for Employees & Suppliers as Source of Innovative Ideas
Q: Where does your company source its ideas for new products, processes, and/or business models?
Part 5: Integration
16 More Than a Third Have Significantly Integrated Organizational Structures
Q: To what extent has your company made changes to its organizational structure in order to create a more integrated enterprise?
17 M4.0 Seen as Key to Enabling Integration
Q: Is there a clear belief that M4.0 technologies and approaches are key to enabling more integrated operations?
18 Increasingly Integrated OT & IT Teams in Last 2 Years
Q: How would you describe the level of
integration between your IT and OT teams?
19 Culture Change Remains Key Challenge to Successful Integration
Q: What are the most significant challenges to improving your company’s integration?
Survey development was led by Executive Editor Paul Tate, with input from the MLC editorial team and the MLC’s Board of Governors.